Raise your hand if you love cleaning up weld spatter.
(We don’t see any hands up.)
Grinding off spatter after finishing a weld is no one’s idea of a good time. But did you know you can limit or even avoid the time and costs associated with spatter altogether? Read on for tips to help you keep spatter at bay so you can spend more time doing what’s important.
The Problem With Spatter
Caused by metal thrown free from the welding point to land on nearby surfaces, spatter reduces efficiency and increases overhead in your assembly line. Welders need to clean up the weld after they’re finished, and excess material is wasted each time.
Many welders consider this part of the territory. Visual cues like sparks or sizzling sounds are the ways many people learn to weld.
“They’re so used to that, and when it’s not there, they question the quality of the weld,” says Chris Sharp, OTC DAIHEN General Manager of Sales and Marketing. “They’re used to welding on sound and seeing the sparks fly.”
The bad news is, these signals are actually signs of an imperfect weld - and they themselves create spatter.
Why would you spend time and money removing part of what you worked so hard to apply? And how do you reach a point of having minimal spatter in your welds? Here are three tips for reducing spatter from your production line welds.
Three Ways to Reduce Spatter
1. Adjust the Arc Voltage
If it's not set correctly, your voltage setting can significantly increase spatter. Low voltage settings will cause spatter because the wire is repeatedly short-circuiting in the weld pool, causing small explosions at the tip of the wire.
This short-circuiting is normal for short-arc MIG welding, but if arc voltage is set correctly, you can typically keep the expelled spatter to a small size and avoid it sticking to your workpiece or surrounding fixtures. On the other hand, a voltage that’s too high can also produce excessive spatter due to extreme arc force.
2. Change the Stick-Out
The amperage of the arc is determined partially by the length of the stick-out, or the amount of wire that is beyond the contact tip that creates the arc.
If the stick-out is too long, it can reduce amperage, throwing spatter out of the weld because it's not penetrating deeply enough into the weld. If it's too short, it increases amperage, throwing material out of the weld due to the force of the arc.
3. Upgrade Your Welding Machines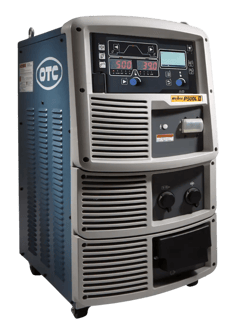
Ever considered that your welding machine - whether manual or robotic - could be causing the problem?
Consider welding machines with special features, such as ultra-low spatter modes to minimize or virtually eliminate spatter. The advanced technology in the OTC DAIHEN Welbee II power source is focused on spatter reduction because of its costly impact.
Cleaner Welds with OTC DAIHEN Welding Technology
OTC DAIHEN has spent decades developing advanced welding power sources for greater efficiency and higher quality welds. The leader in innovation is the Welbee II.
Some of the welding power source top features include:
A Welding Guide with Data Tracking
The on-screen welding guide allows you to select the weld joint, base material and weld size, and the machine provides the suggested parameters for this application.
SMART-PULSE for Mild Steels
The Welbee II SMART-PULSE software, with Artificial Intelligence (AI) control algorithms, produces a flatter weld bead profile, less undercutting, great penetration and reduced spatter with aluminum, steel, stainless steel and exotic metals. The 20ns speed of the computer results in the adjustment of the welding output to either eliminate spatter before it can form or to reduce the size of the spatter.
Special Mode for Low Silicon Solid Wires
The Welbee software provides a stable arc with a good bead appearance and minimal spatter, even on zinc-coated materials that are typically difficult to weld.
Software for Stable Arc on Aluminum
The Welbee II includes software for 5000 series wire on heavy plate to provide a more stable arc, more constant current, good penetration and good bead profile when welding on aluminum.
Synchro Feed Evolution for Robotic Welding
Synchro Feed Evolution is an ultra low spatter welding technology for robotic MIG, MAG and CO2 welding. The technology combines a revolutionary wire retraction system in the torch with a high-speed processor in the power source that together creates minimal spatter and a stable arc.
Hundreds of times each second, the arc is extinguished and the wire advanced and retracted to gently place the formed droplet in the weld puddle without creating spatter. This results in an ultra-low amount of spatter, fine control of heat input and thinner weld application supporting much higher-speed welding.
“During an aluminum welding demonstration I did, we called over an employee to try the Welbee II machine out, and he produced a great-looking weld,” Sharp recalls. “I joked that it was probably the best weld he’d ever created. And he said, ‘I’ve never welded aluminum before.’ When we do aluminum demos with our technology, we get that jaw-dropping effect almost every time.”
Learn More about Welbee Power Sources
Get the complete guide to all the Welbee models and features in our Welbee II Welding Power Source Buyer’s Guide and Comparison Chart.
At OTC DAIHEN, we are your one-stop shop, which means we produce everything you need - welder, robot, torch, wire feeder and all the know-how to put it together and apply it to your toughest welding challenges. Contact your OTC DAIHEN rep today to learn more.