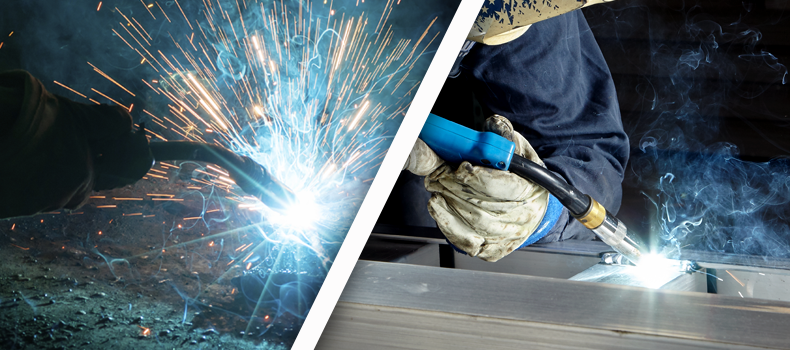
When you're trying to keep production working on a regular schedule without slowdowns in your production line, you often end up weighing the balance between factors that slow down the line and factors that help boost production, but cost more in terms of overhead. Fortunately, there's an easy way to improve your production speed without increasing your overhead too much. In this post, we'll discuss spatter control in your facility: what it is, how it affects your production line and how to implement it with minimal costs.
What is low spatter?
When your production line undertakes welding processes, small bits of molten metal are thrown away from the weld, often landing elsewhere on the work piece outside of the immediate area. Referred to as spatter, it requires additional work to remove from your pieces before they go on for additional finishing work, such as grinding. By using low spatter options and parameters, you can reduce the amount of spatter and therefore reduce the amount of work required before the piece can be moved down the production line.
How does it affect your production line?
By implementing low spatter measures in your production line, you can improve the speed at which the line moves. In turn, this lowers your overhead costs per piece, allowing your company to realize a higher profit on each piece completed and sold. You'll also see a higher quality weld and may see less waste in terms of filler metal that is lost during the production process.
How can I implement it in my design without raising costs?
Though many production line improvements actually end up raising your overhead and production costs to an unreasonable level, controlling excess spatter on your welding production is not one of them. Here are a few simple steps you can undertake to lower spatter on your production line:
- Lower your wire feed speed. A fast wire speed increases your amperage and increases spatter on the produced piece.
- Increase your voltage. Using a voltage that is too low for your situation can increase spatter, so try increasing voltage until you achieve the desired results.
- Lower your stick out. Typically, you want about 3/4" between the tip of the contact and your piece, slightly longer for higher wire feed speeds. Too high a stick out also lowers your shielding gas at the weld, increasing porosity, while also raising the amount of spatter.
- Decrease the work angle. A high work angle increases spatter dramatically. Aim for a work angle below 15º to reduce spatter.
- Ensure all surface contaminants are removed. Oils, paint or treatments in previous production can cause a lot of spatter. Clean the base metal well to get a low-spatter weld.
- Ensure constant wire feed speed. Erratic wire feed can cause random bits of spatter, so make sure your machines are feeding at a constant rate.
- Watch the specs on wire quality. Though it's tempting to buy cheaper wire, you'll lose those savings in post-welding cleanup.
Now that you know the advantages of lowering spatter on your production line and how it can be put into place, why not start implementing these changes into your production specifications? If you need additional information or help selecting welding machinery that will reduce spatter on your production line, please feel free to contact us today. At OTC Daihen, we've spent almost a century helping industry move ahead at the speed of progress.