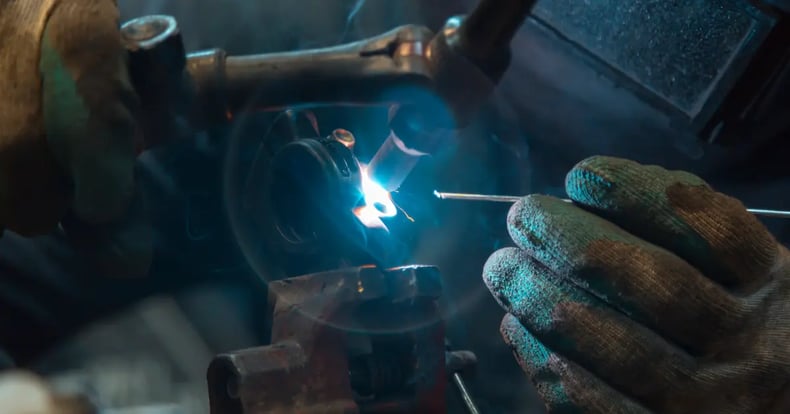
Is the welding wire you're using too small, too large or just right? Welding wire is an essential component of the welding process as it serves as the electrode and filler material, melting and fusing with the base metal to create the joint.
The welding wire diameter can significantly influence the quality of the weld, its strength and the overall efficiency of a welding production line. Choosing the right welding wire is key to production efficiency and cost savings.
5 Factors to Evaluate When Choosing What Size Welding Wire to Use
1) Material Thickness
As a general rule, thicker materials require larger diameter wires, while thinner materials can be welded with smaller diameter wires. The key is to get the correct size filler metal for the application being welded.
Using a wire too small for the material can prolong welding time, raise costs and compromise weld penetration. For a given amount of weld deposit, a smaller wire needs to run at a much higher wire-feed speed than a larger wire. This higher feed speed with a smaller diameter causes more rapid wear on the liners and contact tips. Also, smaller-diameter wires are generally more expensive than larger wires due to the fact that they require more passes in the drawing process.
On the other hand, an overly large wire can reduce precision, leading to fit and quality issues. It may also result in unnecessary cleanup, poor penetration, overlap and porosity.
Another option is to take a look at the welding power source. An advanced power source, such as the OTC DAIHEN Welbee power source, allows welding with thicker wire on thinner material to achieve a high-quality weld.
For example, with the Welbee, you can weld aluminum with 3/64” or 1/16” diameter wires just as if you were welding with 0.030” or 0.035” diameter wire with a competing machine. The larger 3/64” and 1/16” wires are much less prone to feed issues like “birds nesting” and are less expensive to purchase.
2) The Welding Process
The wire diameter can influence the efficiency of the welding process. With the right wire in place, you will produce cleaner welds with minimal weld spatter, resulting in less weld cleanup and wastage.
3) The Welding Position
Follow these basic guidelines for choosing welding wire based on the four main welding positions:
- Flat Position (1G or 1F): This is the most basic welding position where the weld is performed from the top side of the joint, and the face of the weld is horizontal. In this position, larger diameter wires can be used as gravity assists in the deposition of the weld metal.
- Horizontal Position (2G or 2F): In this position, the weld is made on the top side of an approximately horizontal surface and against an approximately vertical surface. A slightly smaller diameter wire might be preferred here to prevent undercut or overlap of the molten pool.
- Vertical Position (3G or 3F): Here, the welding is done on a vertical surface. The challenge is to prevent the molten metal from dripping down. Smaller diameter wires are often chosen for vertical welding because they offer better control over the molten pool, especially when moving upwards.
- Overhead Position (4G or 4F): As the name suggests, this position involves welding from the underside of the joint. This is the most challenging position due to gravity working against the weld pool. Smaller diameter wires are typically chosen to reduce the risk of molten metal falling and to maintain a manageable weld pool size.
4) Desired Penetration
The right wire diameter can significantly influence the achievable penetration, which is the depth the weld metal fuses into the base metal. If deep penetration is required, a larger diameter wire might be more suitable. Conversely, for shallow penetration, a smaller diameter wire is preferable. Balance is key to this: not too small, not too large. Use the correct size wire for the job.
5) Quality
Beyond selecting the correct size, you'll also want to ensure you get the correct alloy of wire to match the base material and service requirements of the project. Purchasing a quality brand of wire is also important. You want consistent diameter, cast, helix and lubrication to make your welding arc consistent. Free wire that clogs liners, fuses tips and causes spatter along with inconsistent welds can cost you a lot of money in the long term.
How to Cut Costs in Welding
Expensive metal-cored and flux-cored wire is often used because it has a wider range of operating parameters and is more forgiving for operators. However, a switch in welding equipment can cut costs in many ways, including the kind and amount of wire and gas used.
For example, the OTC DAIHEN Welbee II welding power source has technology that allows the standard wires to weld with the same appeal as the more expensive wires and gas combinations. There is no need to purchase the more expensive welding wires or gasses for these machines.
Also, the Welbee II creates minimal spatter, which equals minimal wasted wire, less post-weld cleanup including labor and grinding materials. With the Welbee II, a welder can get a deposition rate of nearly 98%, meaning they are laying down 98% of what is coming off the wire spool onto the weld. When ordering wire by train or truckload, costs add up quickly.
Learn More
At OTC DAIHEN, we are your one-stop shop, which means we produce all the hardware you need — welder, robot, torch, wire feeder and all the know-how to put it together and apply it to your toughest welding challenges. Learn more about our Welbee power source models and features in our Welbee II Welding Power Source Buyer’s Guide and Comparison Chart.