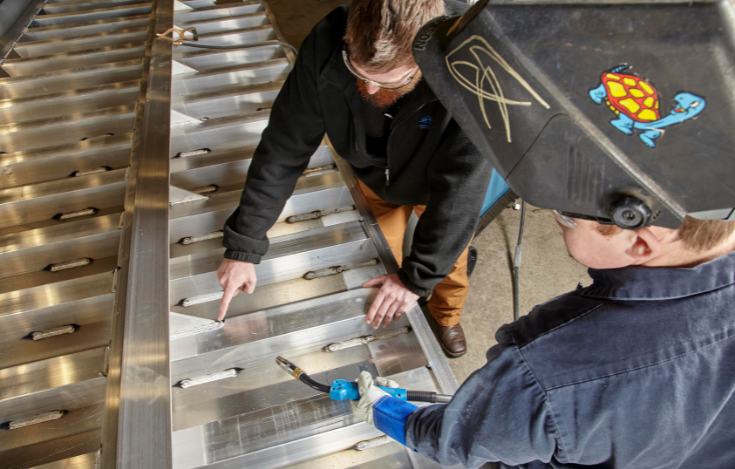
When you're operating a production line, finished quality is vital to the success of your business. Engineers will spend a significant amount of time developing the specifications for your product, including developing the exact welding parameters for each part of the process. But how important are these welding parameters to the quality of the weld and your finished product? Very important!
Using improper parameters can lead to excess weld spatter, creating a need for additional cleanup of welds. A cold weld will sit high above the surface of the metalwork and result in a lack of fusion in the weld root, creating a weak joint and requiring time-consuming cleanup.
What are the Top Welding Parameters to Consider to Produce a High-Quality Weld?
The top welding parameters to take into consideration when arc welding are: amperage, voltage and wire feed speed. All of these can affect the finished weld if these welding parameters are not properly set.
How Do Welding Parameters Affect Weld Quality?
Poor weld parameters can result in a bad weld that has minimal penetration, creating a weak joint in the product, and excessive spatter, which creates additional cleanup work and loss of productivity.
Good equipment, such as a Welbee II power source, can reduce frustration in setting proper welding parameters and help ensure a high-quality, good weld. Welbee II power sources have real-time monitoring of the power supplied to the arc so welders can easily monitor and adjust amperage, voltage and wire speed prior to spatter creation, irregular welds, etc.
![]() |
Bad weld caused by high amps or too low travel speed. |
How Does Amperage Affect a Weld Bead?
Provided that the travel speed is correct, the amperage determines the level of penetration and size of the finished weld bead. The amperage is determined by the thickness of the pieces being welded and dictates the wire gauge used.
Setting amperage below the parameter is likely to give you a tall, narrow weld bead that has little penetration, giving you a weak joint. The weld line will be hard to start and the arc will tend to drift to one side of the joint instead of joining both. If the amperage is set too high, it will give you a bead that is wide, flat and irregular, and it's very easy to end up with excess spatter.
![]() |
Bad weld caused by low voltage. |
Why is it Important to Set the Correct Voltage When Welding?
The voltage determines the profile of the weld bead.
If it's too low, the bead will sit up on the surface of the piece and produce excessive spatter, requiring significant amounts of grinding or cleanup work to flatten the face of the piece and create a possible point of failure due to poor penetration of the weld into the joint.
If it's too high, it will form a wide, flat bead that has inconsistent penetration and poor arc control, providing poor welds in the finished product, and can cause a high amount of spatter, requiring more grinding and cleanup to produce a usable piece. High voltage can also cause sagging welds, and thinner metals may show signs of distortion from the excess heat.
![]() |
Bad weld caused by high voltage. |
How Does Wire Feed Speed Affect the Quality of a Completed Weld?
In MIG welding, the wire feed speed (WFS) determines the current used to create the weld.
Much like the voltage, a WFS that is too high will create a bead that will sit on the surface of the piece and create excessive spatter, requiring significant cleanup, as well as an excessively wide bead with poor penetration and a strong possibility of burn through.
If the WFS is too low, you'll end up with a narrow bead that can take a concave shape, also requiring a lot of extra grinding and clean-up. In general, a 1/4" to 3/8" electrode extending from the tip is about right, but the exact welding parameter will often be further tested and documented by the welding engineer supervising the settings and specifications.
Controlling the Variables in Welding
Controlling the variables in your welding parameters can make a big difference in the quality of your completed welds and the finished product. If your current equipment is causing poor quality and slowing down production, check out the newest features of the Welbee II power sources in this Welbee Welding Power Sources Buyer's Guide and Comparison Chart.
Want more information on Welbee power sources? Contact OTC DAIHEN. We are your one-stop, welding system supplier. We produce everything you need - welder, robot, torch, wire feeder and all the know-how to put it together and apply it to your toughest welding challenges.