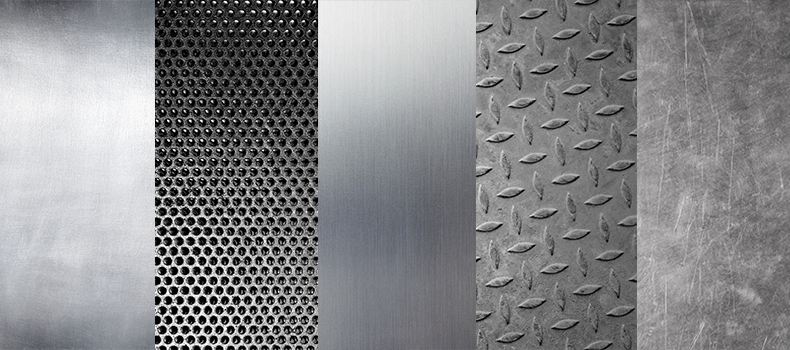
When it comes to creating a long-lasting weld that has strength and integrity, one of the most important factors is the type of filler metal used. But how do you know which filler metal is the best option for your particular situation? Unfortunately, it's not as easy as an A or B answer. In this post, we'll take a good look at different factors that affect your decision so you can select the perfect filler metal for your needs.
Selecting the right filler metal
What's the base metal and what is its quality?
We work with different metals because they have different properties, often ones that don't work well together. Use a filler metal that matches your base metal. Another possibility, though it happens more often in repair than in new production, is the quality of the base metal. If it has a lot of contaminants or similar problems, you may want to look at a filler metal that includes a deoxidizer to force the contaminants to the surface of the weld instead of weakening the entire weld.
What strength do you need to match?
This will depend on the strength of the metal you're welding, but you should always look for filler material that is either the same strength or slightly stronger than the material around it.
What kind of equipment are you using?
If your equipment doesn't have sufficient amperage for the wire you're considering, you will either need to find a smaller diameter wire, which will slow down your production line, or obtain a machine that operates at a higher amperage.
What position are you welding in?
Filler metals that are developed for horizontal welds are usually the strongest, with the lowest porosity. But if you have a design that requires you to weld in a different position, make sure you use a filler metal that meets that position's needs.
Are there design or regulatory specs that need to be met?
Another way of approaching this is by asking what are the environments where the weld will be exposed? If the weld will be under vibration or stress, make sure your filler metal meets that need. If it will be exposed to water, pressure or hot environments, those also need to be taken into consideration.
What shielding gas is needed?
If you're using straight carbon dioxide to shield the weld, you'll get deeper penetration of the weld, but often at the cost of more spatter. If you're adding argon to the mix, more of the filler metal may transfer into the weld and you'll have consistent weld quality and lower spatter.
Do you need a heat treatment before or after welding?
Many welders know that when working with thicker metals and some types of steel, the metal should be preheated for the best welding results, to avoid shrinking in the weld and possible cracking issues as the entire piece cools as one. But some materials also require heat to slow the cooling process. If your project requires these types of metals, make sure your filler metal will work with the extended cooling period.
By bearing in mind the different factors your project requires, you'll be able to find the right filler metal for your exact needs. If you need help selecting the right equipment for your job, please feel free to contact us today. With almost a century of experience, we have a strong knowledge and experience base to help your production facility succeed.