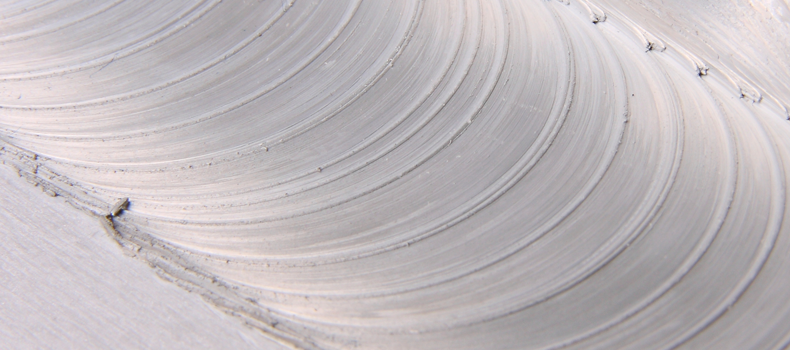
As our technology advances, our industry is rapidly changing. Some welding developments provide a serious advantage while others don't actually work out in the end. But which innovations should you ignore and which ones should you implement? It's a tough decision, but here's our take on the most important recent developments in welding that deserve some attention.
- Steel Friction Stir Welding: This type of weld is produced using a stirring probe that rides below the shoulders of the tool that holds it. As the probe and tool spins, it creates a solid-state joint that has fewer issues with corrosion, porosity and similar issues inherent with poor-quality welding. However, the speed of rotation and travel must be modulated to prevent flaws from forming along the line of travel and the current maximum weld length is 30 cm, too short for many applications. Assembly line workers would probably also need additional education in this method, causing additional costs and a learning curve that may show up in production, leading to additional quality control issues, lower production and similar concerns while implementing this type of process.
- Ultrasonic Inspection of CRA Welds: As corrosion resistant alloys (CRA) become more common in welding, especially the pipeline industry, knowing how to inspect these welds for potential faults is vital to ensuring the safety of the completed equipment. Using ultrasonic machinery to inspect the weld overlay deposition, welds can be checked from the outside of the pipeline. The metals content of the CRA can, however, cause degradation of performance to the point of being very difficult if not almost impossible to interpret. Currently, several companies are undergoing research and development to perfect this weld inspection method.
- Strong Market Growth: As our world continues climbing out of the worldwide economic depression that it had sunk into, demand and production is expected to continue to surge. With a heavy focus on construction and metal manufacturing, it's expected that welding companies, suppliers and shield gas providers will see significant growth for at least the next five years. According to a new report by RnR Market Research, it's expected that shielding gas industries alone will see an estimated growth of 5.7% CAGR until 2020, growing from 7.17 billion to 9.42 billion by that time. This is reflected in other areas of the industry as well, including production reports, future order statistics and similar indicators. As governments at all levels are increasing spending to take care of problems that were put on the back burner during the recession, the welding market will see significant growth.
By implementing new developments into your production line, you have the ability to keep your business at the cutting edge of technology. In turn, these improvements help you keep your business productive with a lean overhead that keeps you competitive. At OTC Daihen, we believe in providing not only the most cutting-edge welding machinery your company needs, we also provide the training you need to implement it into your production facility. Please feel free to contact us today for more details about how we can help you integrate these welding developments into your assembly line.