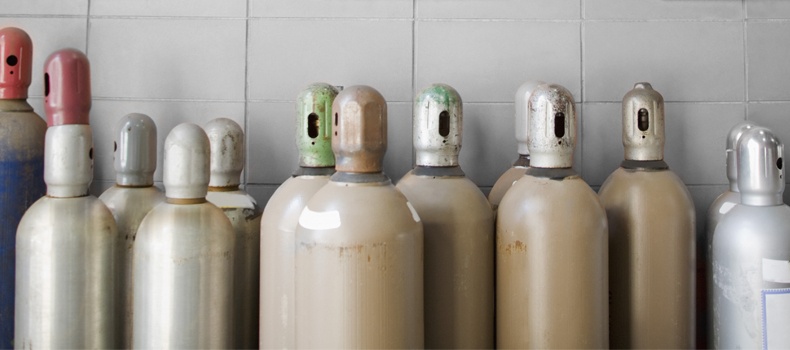
The shielding gas used during a weld is a key component in its success, much like the welding technique used, the skill of the welder and the filler material. In spite of the crucial nature of choosing the right shielding gas, too many welders go about such a decision haphazardly, without giving it much thought. The benefits of choosing the right gas the first time, though, can run the gamut of better welds, more dependable productivity, increased quality and lower costs.
The Big Four
During the welding process, there are four gases that are used most often in the shielding capacity -- oxygen, argon, carbon dioxide and helium. Each of these gases has its own unique factors and characteristics, such as the particular weld arc stability, proprieties desired, costs and availability, which are all considerations when it comes to choosing the right shielding gas.
Oxygen (O2)
Oxygen is a reactive gas and often used in a ratio of nine percent and under. When combined with argon, a host of benefits are obtained, including arc stability, weld pool fluidity and weld penetration. These advantages are most evident when welding materials such as low alloy, stainless steels and carbon. Oxygen is responsible for weld metal oxidation so avoid its use with copper, aluminum, magnesium and other like metals.
Argon (Ar)
Argon provides stable arc features, making it the ideal shielding gas for use with metals like titanium, magnesium and aluminum. When welding carbon steel, combining argon with carbon dioxide -- standard mixtures range from between 75 and 95 percent argon with 5 to 25 percent carbon dioxide -- is an ideal shielding gas. The benefits realized by this combination include a reduction in post-weld cleanup, consistency in both appearance and weld quality as well as ideal control of the weld pool. Due to its confined penetration profile, argon is crucial during butt and fillet welds.
Carbon Dioxide (CO2)
While carbon dioxide has a number of advantages over other gases, it also has some drawbacks as well. In addition to being the least costly gas used to weld carbon steels, CO2 is also the most popular reactive gas used during the welding process. Another advantage of using carbon dioxide is that it does not need an additional inert gas. When presented with thick material that must be welded, carbon dioxide is the preferred shielding gas as it allows for a deep weld penetration.
Carbon dioxide has a historical reputation of increasing spatter. However advancements in arc welding machine technology has drastically reduced the generation of spatter when welding with 100% CO2, and these economical machines are capable of welding even very thin sheet carbon steels.
Helium (He)
When a weld of non-ferrous materials is needed, helium is often the shielding gas chosen. Helium is also often added to argon with carbon dioxide to weld stainless steel. Producing a deep and wide penetration profile, helium is often used for thick materials. Typically, helium is used in ratios of 25 to 75 percent with the balance being argon. Helium is more expensive than other shielding gases and needs a higher flow rate than argon. Before using helium, welders need to ensure any benefit offsets the additional cost.
The brief overviews of each gas presented serves as a basis for choosing the right shielding gas for your project. Contact OTC Daihen for more information about this welding topic or the advancements in arc welding technology available in all OTC Daihen products.